- 2021年7月9日
- 更新日:2025年6月29日
-
真空注型についてご紹介いたします!
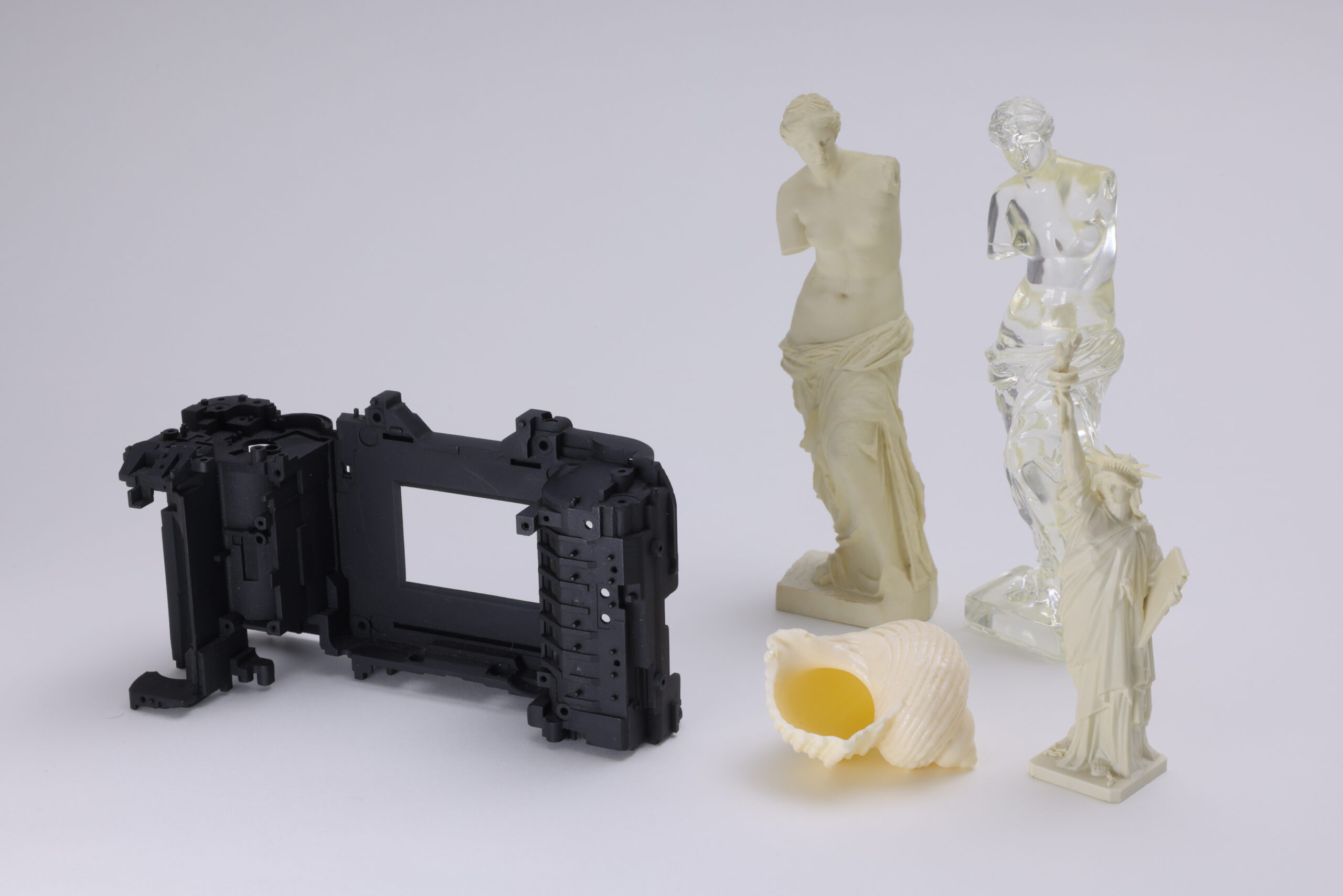
こんにちは!
今回はプラスチックの成形技術、真空注型についてご紹介します。
真空注型とは?
真空注型とは、今から約40年前の1980年頃に工法が確立されたと言われているプラスチックの成形技術のひとつです。
従来、プラスチック製の部品を数十個以上製作するには、高価な金型を製作するしかなかったのですが、真空注型の登場により安価なシリコーン型で成形品を製作できるようになりました。
真空注型の製作工程
1.マスターモデルの製作
光造形(3Dプリンター)や切削加工でマスターモデルを製作します。
光造形の場合は積層による段差ができる為、外観の仕上げ作業を行います。
その後、マスターモデルのPL(パーティングライン)にテープを貼り、ゲート棒を取り付けます。
2.型枠の製作
樹脂板で枠を製作し、マスターモデルをセットします。
その際、ガス抜き棒をマスターモデルに接着します。
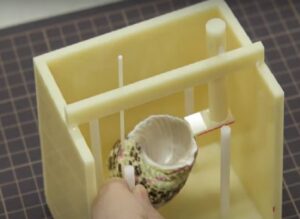
3.シリコーンゴムの充填
シリコーンゴムの主剤と硬化剤を計量し、混合します。
混合時に発生した空気を抜く為に、真空脱泡をします。
脱泡したシリコーンゴムを②で製作した型枠に流し込みます。
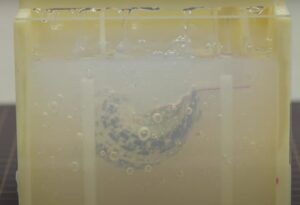
4.型割り
③でシリコーンを流し込んだ型枠を乾燥炉に約1日入れて硬化させます
硬化したら型枠をすべて外します。
すると、マスターモデルが埋まったシリコーンのブロックが出てくるので、PLに貼ったテープを目印にナイフで切開します。
マスターモデルを取り出したらシリコーン型の完成です。

5.成形準備
4で完成したシリコーンゴム型をテープで巻いて固定します。
6.材料の充填
2液混合性のウレタン樹脂の計量・攪拌・脱泡を行います。
真空注型機に入れ、⑤で準備したシリコーンゴム型にウレタン樹脂を流し込みます。
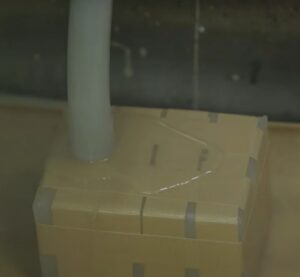
7.樹脂硬化
6でウレタン樹脂を流し込んだシリコーン型を乾燥炉に入れて、樹脂を硬化させます。
大きさによって変動しますが、約1時間~2時間で硬化します。
8.脱型
ウレタン樹脂が硬化したらシリコーン型を乾燥炉から取り出します。
テープを剥がして型を割り、中の硬化した注型品を取り出します。
9.完成
取り出した注型品のバリ・ゲート部・ガス抜き部の仕上げをすれば完成です。

真空注型の製作工程は以上です。
1個の部品を作るのに1~2時間かかる為、1日の生産数量は5~6個程度です。
また、1つの型で生産できる上限は約20個です。数個~数十個の生産に向いている加工方法です。
真空注型のメリットとデメリット
真空注型のメリット
- イニシャル費(シリコーン型費)が安価
- マスターモデルがあれば3Dデータがなくても製作可能
- ゴム部品(ウレタンゴム)の加工も可能
- 短納期対応が可能
- 抜き勾配がほぼ不要(無理抜きも可能)
- 金型設計が不要
真空注型のデメリット
- 1型で20個程度しか成形できない
- 精度がやや劣る
- 材料がウレタン樹脂・エポキシ樹脂しか使用できない
真空注型の用途
真空注型はインサート成形・アウトサート・透明部品・調色品・シボ風・2色成形も可能で、食品衛生法を取得している材料やV-0材料にも対応しており、様々な業界の少ロット量産に活用いただけます。
また、アクリル樹脂を切削して製作するアクリル型では、シリコーンゴム製品の成形も可能です。
電子部品の試作・車載部品の試作・フィギュア・医療機器・測定機器などの試作検討案件や年間数十個の量産品にも使用することができ、低コスト・短納期を実現可能です。
現在、3Dプリンターが普及し、個人でものづくりをされる方も増えています。ガレージキットなど、マスターモデル・シリコーンゴム型を製作し、成形・販売などされる方もいます。一般のお客様も注型でものづくりを楽しみ、製作品を展示会やインターネットでも販売されている方々は数多くいらっしゃいます。
幅広い業界で、様々な用途で注型は活躍しています。
真空注型でのご検討や分からない事がありましたら、お気軽にご相談ください!
“加工のすすめ”とは?
株式会社ニッシリが運営する加工技術のご提案サイトです。
当社が70年間で培った製品知識や加工技術を元に、お客様の加工のご要望に寄り添います。『素材の試作や小ロット量産をしたい』『コストカットをしたい』『企画段階からサポートしてほしい』など、様々なご要望に対応させていただきます。